What is inventory management?
Inventory management is the combination of processes used to manage the supply of equipment, materials, and other resources in the lab. Some key components of inventory management include tracking and ordering, checking availability, locating storage, managing audit logs to check consumption, predicting future needs, and managing safety information.
Proper inventory management is essential to an efficient laboratory. When inventory systems fail, labs can run out of materials, resulting in schedule disruptions and lowered productivity. Over-ordering can have adverse effects, too, such as wasted resources.
In this piece, we look at the importance of proper inventory management. We also examine how to optimize laboratory operations through efficient inventory management systems.
Issues and challenges associated with inventory management
While proper inventory management makes sense, it’s not always straightforward. Some of the main challenges faced in today’s labs include:
- Low predictability: Some organizations strive to have their labs follow lean manufacturing processes. This strategy eliminates waste and improves efficiency. However, it relies heavily on process consistency, which is lacking in many laboratories.
- Poor use of time: Between stocktaking, ordering, and a large volume of associated administrative work, inventory management can take significant time away from a researcher’s primary role as a scientist.
- Lack of consistency: Labs across an organization might follow completely different processes. For example, each lab might require different minimum stock levels or a unique order sign-off procedure. These discrepancies can confuse internal departments as well as vendors.
- Supply chain issues: Even the best inventory management systems can get hit by supply chain issues. This is a particular issue when taking a just-in-time (JIT) approach and is one of the main reasons many laboratories opt instead for a just-in-case (JIC) system.
How lab redesign is achieved through efficient inventory management
Many lab managers see the benefits of outsourcing their inventory management to third parties. Advancements in software and inventory management infrastructure components such as sensors and tracking devices also make fully automated systems increasingly accessible.
Here are some of the central components of a comprehensive inventory management system:
Cloud-based software
Cloud-based platforms forgo paper, excel spreadsheets, and complex email chains. Cloud-based systems enable staff to easily check stock of a particular item and order replenishments in just a few clicks. This helps to free up time for other work and ensure scientists always have all the resources they need. Some platforms will enable you to set minimum and maximum inventory amounts to ensure that items are consistently available.
Quartzy is one popular cloud-based system that helps labs manage procurement. This software enables you to track data such as quantity, location, physical properties, and expiration dates for all items. It facilitates product ordering and includes price comparisons. ChemInventory is an interesting alternative. While its ordering system isn’t as advanced as that of Quartzy, it does offer the option to search for chemicals by structure.
Genemod is another cloud-based inventory management platform. Designed specifically for lab freezer management, Genemod enables users to track the status of every reagent, sample, and asset in the lab’s freezers, in real time. A virtual freezer matches its physical counterpart, so a glance at the interface tells you exactly which items are on every shelf. This can be a useful tool to help avoid staff having to dig through temperature-sensitive samples and reagents by hand.
Another perk of cloud-based inventory management is its integration capabilities. Platforms can often be integrated with other popular software such as lab notebooks or accounting apps, further boosting productivity. Colabra has an inventory management system that integrates with scientists’ experimental notes.
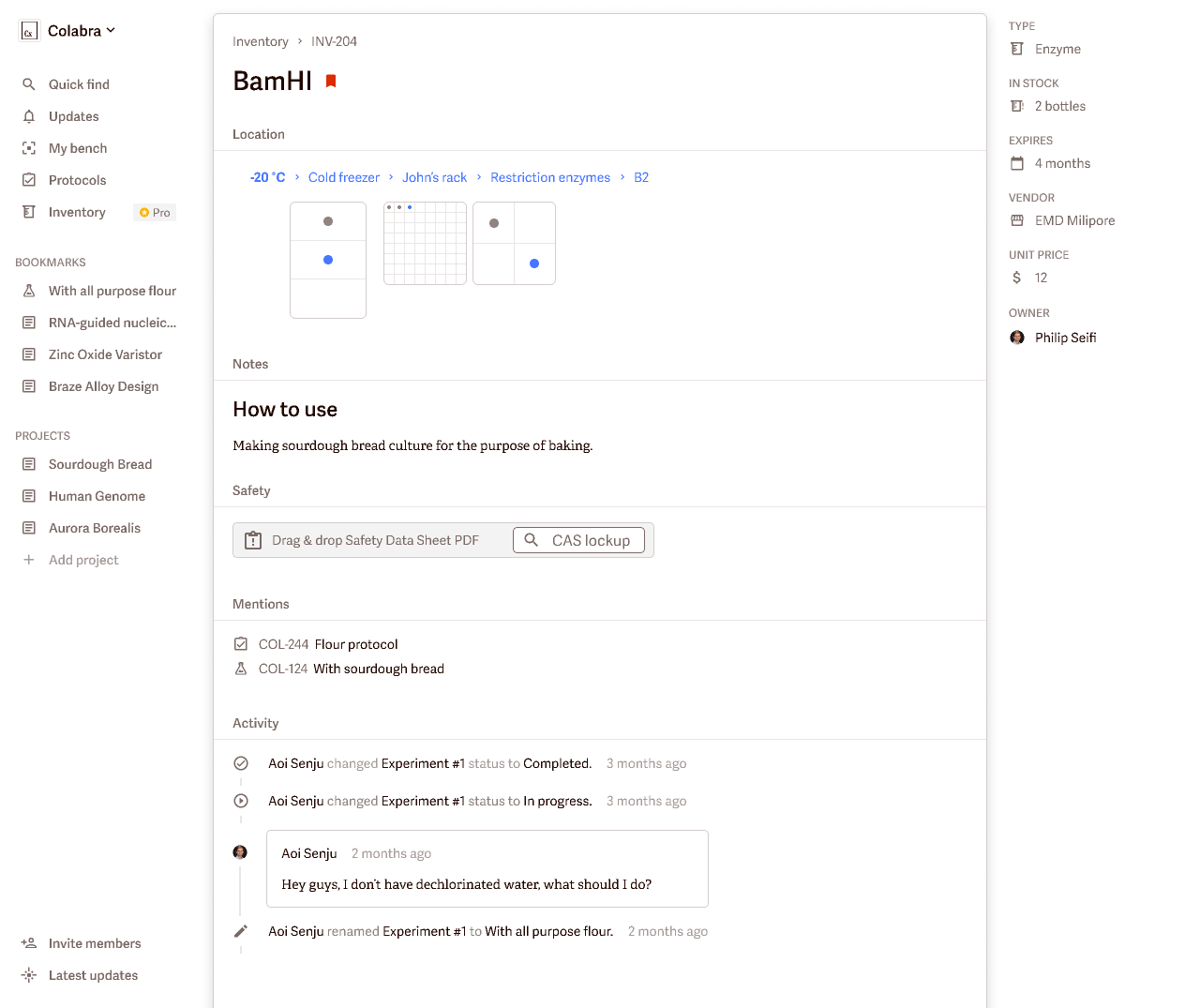
The Colabra inventory manager interface.
When deciding which cloud-based platform to use, it’s important to consider which features are most important to your operation, and compare other factors such as cost and ease of use. ChemInventory could be ideal for smaller teams on a limited budget looking for a way to organize chemicals. For teams prioritizing purchase orders, Quartzy may be best, and for teams looking for closer integrations with the experiments themselves, Colabra may be best.
Automation and connectivity
Many storage systems have taken a step further in recent years with the installation of smart shelves that use sensors to detect the addition or removal of items. Each time an item is removed from a shelf, an automated request can be prompted to replenish that item.
Atellica Inventory Manager uses radio frequency identification (RFID) for real-time inventory tracking across multiple laboratories. When the stock of an item reaches a critical level, the software submits an order request. It even provides expiration date alerts, so labs are never left scrambling to replace out-of-date stock.
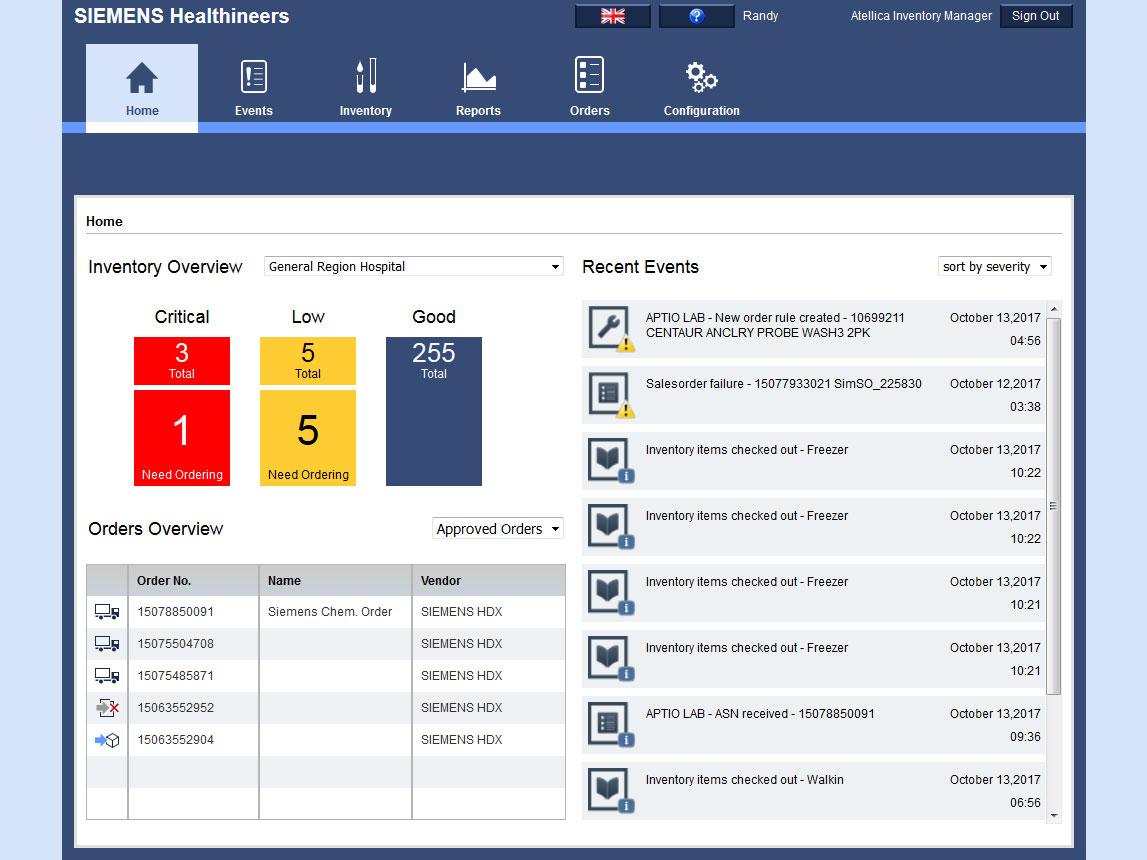
The Atellica inventory manager interface. Source: Siemens Healthineers
AI and machine learning
A key benefit of automated cloud systems is that every action is closely tracked. This provides a wealth of data that can be utilized to refine processes further. For example, analyzing the frequency with which an item is picked or ordered allows for better demand predictability and waste reduction.
A recent study showed that learning-based inventory management could provide demand prediction accuracy of over 80 percent and reduce inventory costs by 25 percent compared to other methods. The potential for AI doesn’t stop at the ordering stage. Robots can be deployed to take over many of the arduous manual tasks involved in inventory management, such as locating, picking, labeling, restocking, and more.
What improved inventory management means for the future
Effective inventory management minimizes waste, which is particularly important when dealing with toxic or reactive materials, or non-recyclable resources such as PPE items that might expire before use. Moving to cloud systems can also eliminate paper and electronic waste.
Redesigning laboratories with effective inventory management can have a significant human impact, too. There are benefits to increased productivity from not having every scientist perform double duty as an inventory manager, allowing them to focus on the core research at hand. What’s more, automated cloud systems can enhance collaboration efforts and improve interdepartmental relationships by allowing real-time communication across a centralized interface.